Overview
As a leading fabricator of custom gearboxes for the aerospace industry, Gateway Engineering requires high-performance, precision magnetic seals built for extreme temperatures and high altitudes.
When Gateway's engineers reached out to Ergoseal for urgent help addressing issues with their current seal, we were able to quickly complete testing and deliver a custom solution that worked perfectly for GE and their customers.
There was a unique opportunity to collaborate on a best-fit solution.
Gateway had worked very hard over the last several years to move away from their existing magnetic seal supplier, due to lead times and minimum quantities, not to mention cost.
Leo Harisiadis • Vice President of Sales, ErgosealFinding a magnetic seal fit to be used in more designs
Gateway Engineering is a leader in the field of speed increasers and reducers. They are well-regarded in the industry for fabricating custom gearboxes, often for the aerospace industry.
In January 2021 Gateway Engineering reached out to Ergoseal for a custom solution to address issues with an existing magnetic seal. After a preliminary discovery call with our sales team, we provided our corporate snapshot document and seal design data sheet to highlight our capabilities and collect design inputs for our seal proposal, respectively.
The inquiry details provided both companies a unique opportunity to collaborate on a best-fit solution. According to Gateways engineer, the company had “worked very hard over the last several years to move away” from their existing magnetic seal supplier due to “lead times and minimum quantities, not to mention cost.” Further, they sometimes encountered puzzling leakage issues. The engineer was looking to work with the Ergoseal team to develop a more standard seal that they could incorporate in more of their designs.
Provide a feasibility report to verify design performance
Ergoseal began work on this project by reviewing the operating conditions and seal requirements for the subject application: a temperature altitude chamber gearbox and extension shaft. Its two-inch-diameter shaft rotational speed peaked at 30,000 revolutions per minute. Temperature and pressure conditions simulated altitudes up to 65,000 feet of elevation — about 14 pounds per square inch pressure differential and temperature range from 100 °C to -60 °C. Based on these design inputs, we identified an existing mechanical face seal that would facilitate quick and inexpensive turnaround to satisfy their urgent need for working seals.
However, to verify the existing design would meet this new application’s slightly more demanding conditions and requirements, Ergoseal proposed preparing a Feasibility Study and Advanced Verification (FSAV) report for the customer. They agreed, though time was of the essence. Over the next few days, we evaluated predicted performance of the existing design in the new application using finite element analysis and face-seal-specific simulation software. Then we quickly provided a report predicting that the running torque, power consumption, temperature distribution, and fluid migration across the seal would all be within limits — assuming an adequate lubrication condition — which we highlighted as the largest source of uncertainty based on customer inputs.
Passed with flying colors
Upon subsequent order and shipment of samples, initial seal testing was completed. Test results and analysis of the returned seals were encouraging but mapped onto our predictions when assuming inadequate lubrication conditions. Per Ergoseal’s guidance, the customer routed more oil to the mechanical face seal, circulating heat away from the seal interface.
We also took the opportunity to modify the secondary seal elastomer and mating ring adapter geometry, further customizing the design slightly in response to our analysis of the returned seals. With these judicious enhancements based on corroboration between verification via simulation, validation via testing, and overall customer feedback, the subsequent iteration of the seal passed with flying colors. According to customer testimony, “GE came to view witness testing of the gearbox and chamber extension shaft last week. They are happy and us approval to ship the system to them… Also, we have no complaints from Pax River, and they have been running for several months now. Thanks to you and your team for all of your help. We couldn’t have made it without your close support… I appreciate all you do for us!”
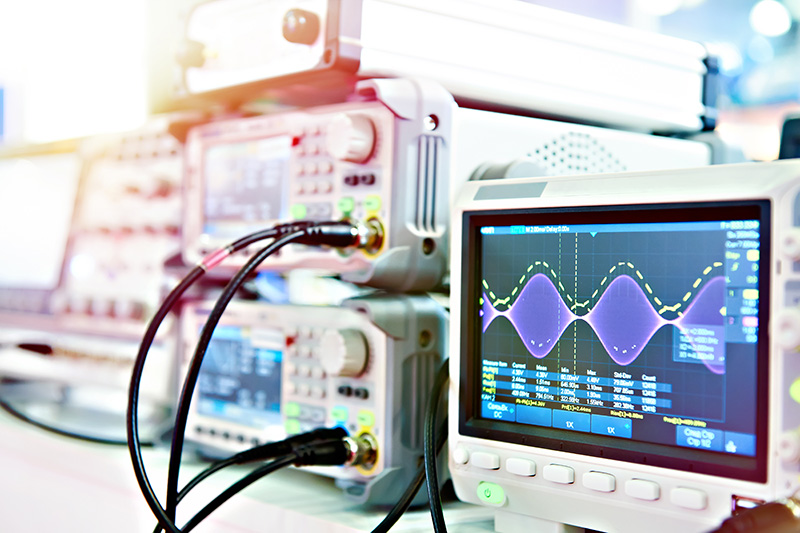
We couldn’t have made it without your close support
GE are happy and gave us approval to ship the system to them… Also, we have no complaints from Pax River, and they have been running for several months now. Thanks to you and your team for all of your help. We couldn’t have made it without your close support… I appreciate all you do for us!
Engineer, Gateway EngineeringHave a project? Tell us how we can help.
Our seal design and engineering department have expertise in a wide variety of sealing solutions to help you find your perfect solution.