Case Study: Cost-Efficient and Reliable Seal Replacement for Vapor Recovery Blowers
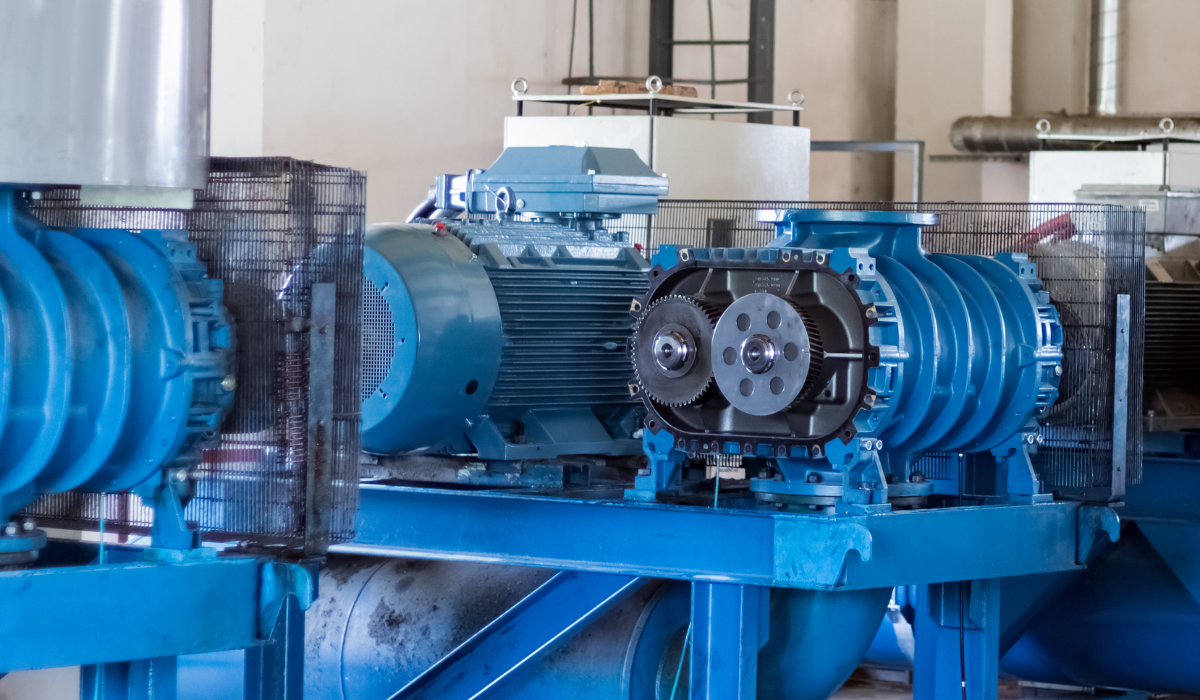
Overview
When reliability is critical, innovation drives solutions. A client with a vapor recovery application faced recurring seal failures caused by blistering, coupled with high costs and lengthy lead times for replacements. Their existing third-party bellows seals were both failure-prone and expensive, leading them to turn to Ergoseal for a better solution.
Leveraging their expertise, Ergoseal developed a custom Type 11 seal featuring their HE-10 carbon grade, known for its resistance to blistering in demanding applications. This solution not only resolved the failure issue but also significantly reduced costs and lead times. This case study highlights how Ergoseal’s innovative approach addressed the client’s challenges and delivered measurable, long-term results.
Bellows seals are frequently specified where they are not necessary.
In these applications, Ergoseal can design and manufacture a drop-in replacement that is typically on the order of half the cost and half the lead time of bellows seals at an equivalent quantity.
Bryan Callaway • Design Engineer, ErgosealPreventing seal failure due to blistering plus cost/lead time issues
A client with a vapor recovery application faced recurring seal failures in their blower systems. The primary issues were:
- Blistering Failures: Their existing third-party bellows seals were prone to blistering, a common failure mode in this application.
- High Costs and Long Lead Times: The seals were expensive and had extended turnaround times, impacting operational efficiency.
The client sought a reliable, cost-effective solution to reduce failures and improve accessibility to replacement components.
Measure critical features; install and test proposed alternatives
Ergoseal developed a tailored solution to replace the failure-prone seals with a more reliable and cost-effective alternative. This took place in five phases:
- Initial Assessment (May 2023): Ergoseal proposed a Type 11 seal design as a drop-in replacement. They delivered a preliminary design proposal and quote by early June.
- Design Revisions and Restart (October–November 2023): After a period of inactivity, the client re-initiated the project on October 4, 2023. Ergoseal updated the design based on new client insights and confirmed the quote by mid-October and finalized the purchase order on November 3, 2023.
- Production and Delivery: Ergoseal completed production and shipped the seals by February 1, 2024.
- Troubleshooting and Support (April–May 2024): Upon installation, the client reported severe leakage in April 2024. Ergoseal identified and corrected an installation error during an on-site visit, restoring functionality.
- Validation and Success (August 2024): The seals underwent two months of rigorous testing where they were being used in the field. By August 23, 2024, the system was confirmed to operate flawlessly.
An innovative solution that delivers plus cost and lead-time savings
Instead of simply replacing the incumbent seals with similar ones, Ergoseal took a different approach that not only solved the seal failure issue but saved their customer considerable time and money.
A key takeaway: Bellows seals are often over-specified for applications like this. Ergoseal demonstrated that their customized Type 11 seals can achieve equivalent or superior performance at a fraction of the cost and lead time. Their HE-10 carbon material is a proven solution for addressing blistering in challenging mechanical seal installations.
- Cost Savings: The Type 11 seals provided a 50% reduction in both cost and lead time compared to the previous bellows seals.
- Enhanced Reliability: The new seals resolved blistering issues thanks to Ergoseal’s HE-10 carbon grade.
- Client Confidence: The successful resolution led to additional orders, including another bellows seal replacement for a sister company within the client group.
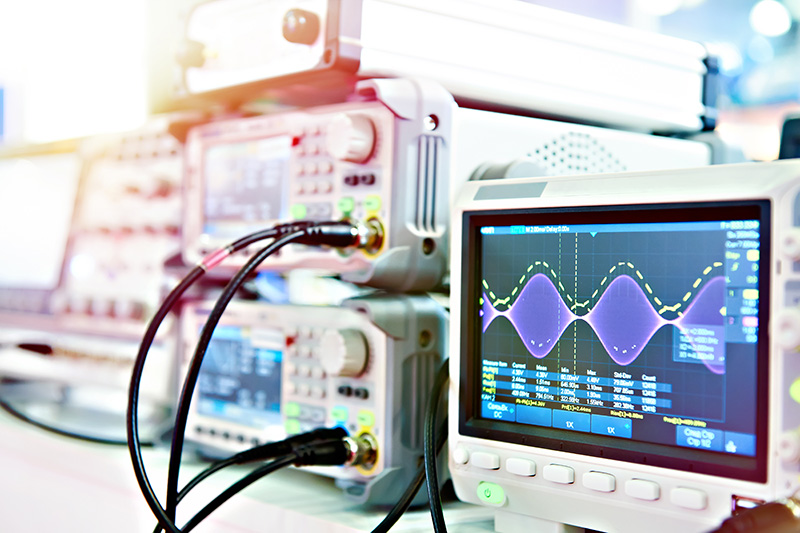
We got the first pump installed about 2 months ago.
It’s been running without issue, have been getting back good oil analysis results with pretty much no contamination as of yet.
The… seals… seem to be working great. We have been seeing a reduction in contamination of the oil from the monthly oil samples.
Confidential ClientHave a project? Tell us how we can help.
Our seal design and engineering department have expertise in a wide variety of sealing solutions to help you find your perfect solution.