Case Study: Custom Seal Solution for Aircraft Wheel Speed Sensors
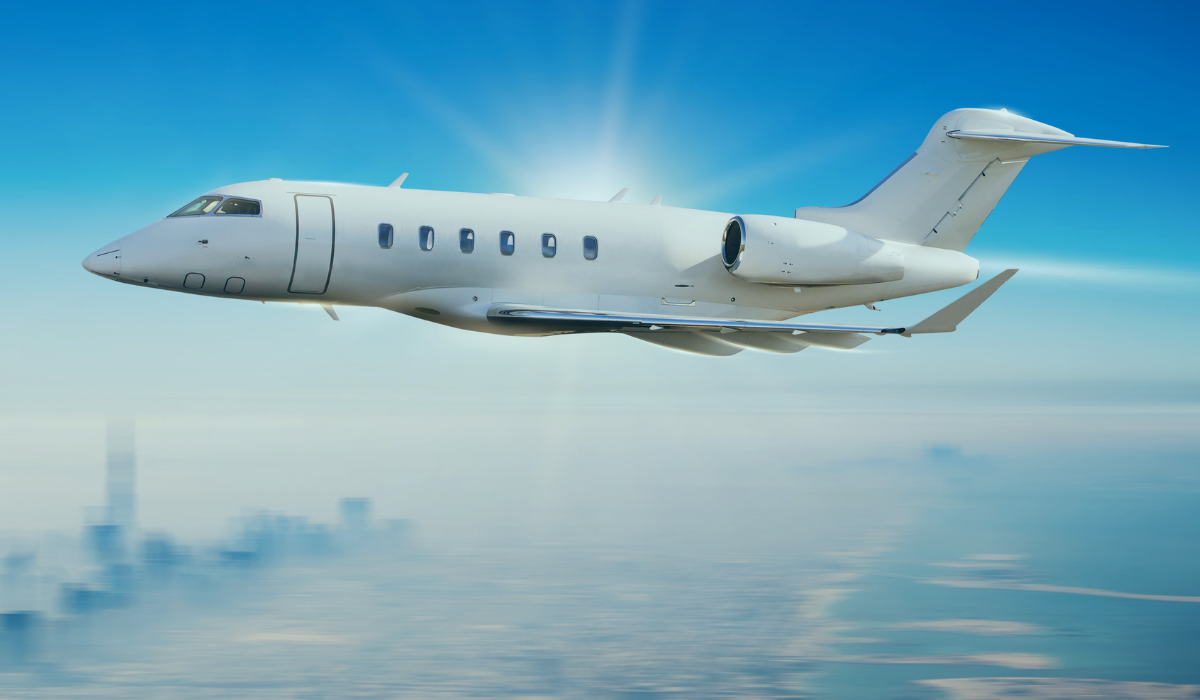
Overview
A leading manufacturer in the aerospace industry, specializes in high-performance aircraft used for both commercial and military applications. Their aircraft rely on precise engineering and advanced sensor systems to ensure accurate speed monitoring, efficient braking, and overall flight safety.
One critical component in this system is the wheel speed sensor, which provides real-time data on wheel rotation to support braking control and anti-skid functions. These sensors require high-performance seals to protect them from extreme conditions, including high pressures, temperature fluctuations, and exposure to contaminants.
IT WAS VERY IMPORTANT TO FIND A SOLUTION
because the customer's existing product was discontinued and they had no other alternative. Gerald Strenk • Global PTFE Product Manager, ErgosealA Discontinued Seal Threatens Aircraft Safety
When a key supplier discontinued a crucial seal used in their wheel speed sensors, this manufacturer needed a reliable replacement — one that could maintain their performance standards without requiring system modifications.
The wheel speed sensor plays a critical role in aircraft braking and safety systems by measuring the rotation speed of each wheel. This data is essential for anti-skid braking systems (ABS), ensuring that braking power is distributed evenly and preventing dangerous skidding or wheel lock-up during landing.
This manufacturer faced a significant supply chain issue when their current seal supplier discontinued a critical part number used in these sensors. The seal protects the sensor’s internal components from high temperatures, pressure changes, and contaminants, ensuring accurate speed readings and long-term reliability. Without it, the performance of the entire braking system was at risk.
Finding a suitable replacement was urgent, as sourcing a new supplier with the expertise to design a precise, high-performance alternative was not an easy task.
A Custom-Engineered Seal Replacement
- Analyze the existing seal by examining a spare part sent by the customer.
- Gather all necessary application data, including environmental conditions, performance expectations, and material compatibility.
- Design a custom-engineered replacement seal that met or exceeded the original part’s specifications.
- Manufacture and test the seal in-house, ensuring it could withstand the rigorous demands of aircraft operation.
By leveraging our onsite engineering, testing, and manufacturing capabilities, we delivered a customized solution that provided the same fit and function as the discontinued part — while improving long-term durability and performance.
Improved Performance, Reliability, and Supply Chain Stability
By working with Ergoseal, the aircraft client successfully replaced their discontinued seal with a custom-engineered solution that met all performance and durability requirements. The transition was seamless, ensuring that their wheel speed sensors continued to operate with precision and reliability.
Beyond simply replacing the discontinued part, the new seal provided several key advantages that improved long-term efficiency and supply chain security:
- Seamless replacement – The new seal was designed and produced without requiring modifications to the customer’s existing system.
- Improved durability – The updated design and materials extended the seal’s lifespan, reducing long-term maintenance needs.
- Supply chain security – The customer no longer had to worry about discontinued parts disrupting operations.
- Faster turnaround – Ergoseal’s in-house capabilities enabled a quick and cost-effective solution, minimizing downtime.
When critical components become unavailable, having a trusted engineering partner makes all the difference. Ergoseal’s expertise in custom sealing solutions ensures that customers can continue their operations without interruption — while even improving performance and reliability in the process.
Need a custom-engineered seal to replace a discontinued part? Get in touch with our team today.
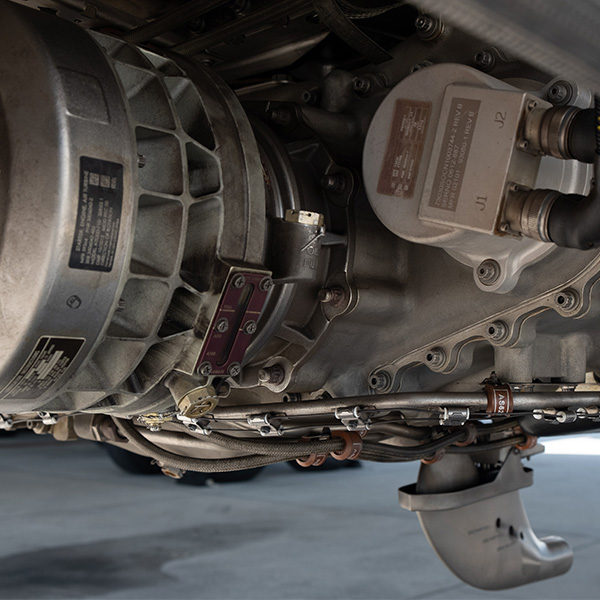
THIS WAS COMPLICATED BECAUSE WE ONLY HAD A USED SEAL TO REPLICATE.
This design was from scratch and the seal was very small — .419” diameter.
Gerald Strenk • Global PTFE Product Manager, ErgosealHave a project? Tell us how we can help.
Our seal design and engineering department have expertise in a wide variety of sealing solutions to help you find your perfect solution.